What is the secret of ultradurable Roman concrete?
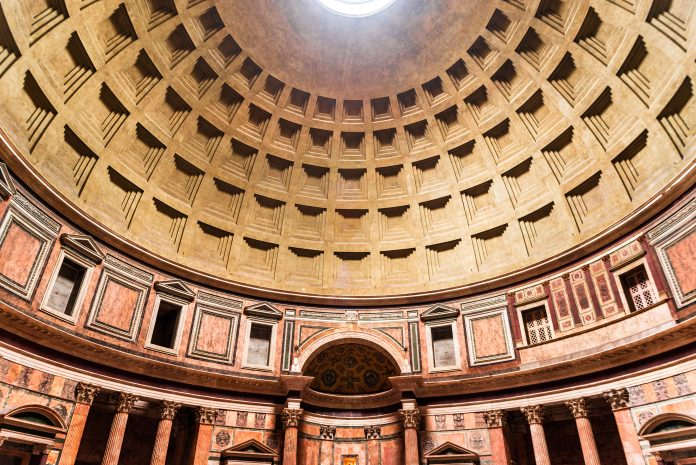
The Pantheon is the world’s oldest structure at 1,898 years old; but how has it stood the test of time? Roman concrete is the answer
The Ancient Romans were masters of many things, including engineering and constructing vast networks of roads, aqueducts, ports, and massive buildings. Perhaps the most amazing thing is that these remains have survived for two millennia. But why?
By means of comparison, some modern concrete structures have crumbled to the ground after only a few decades. In contrast, Rome’s famed Pantheon, the world’s largest unreinforced concrete dome, was dedicated in A.D. 128 and is still intact.
Along with this, some ancient Roman aqueducts still deliver water to the city of Rome today.
How is it possible that the oldest building in the world, the Pantheon, still stands at 1,898 years old?
How is it possible that the oldest building in the world, the Pantheon, still stands at 1,898 years old? Scientists believe roman concrete is the answer.
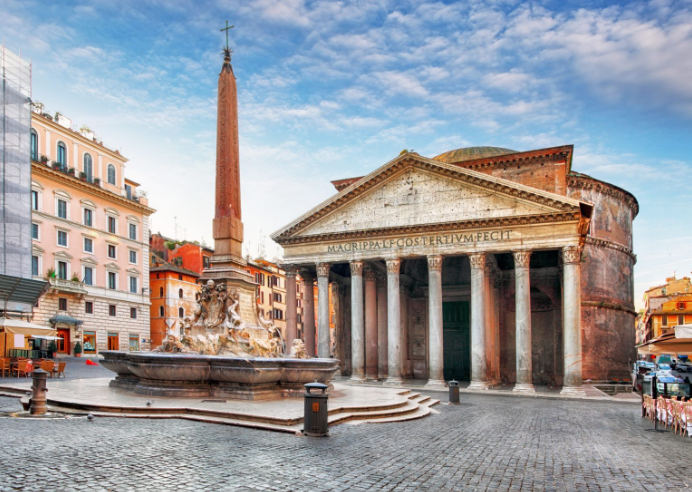
Researchers spent decades trying to figure out Rome’s secret
Naturally, researchers from around the world have been fascinated by the ancient Roman structures that survive to this day. And they have spent decades trying to figure out the secret of this ultradurable ancient construction material.
They have been particularly interested in structures that endured especially harsh conditions, such as docks, sewers, seawalls and seismically active locations, and how they stood the test of time.
ancient concrete-manufacturing strategies incorporated several key self-healing functionalities
Now, a team of investigators from MIT, Harvard University, and laboratories in Italy and Switzerland, has made progress in this field. They have discovered ancient concrete-manufacturing strategies that incorporated several key self-healing functionalities. The MIT researchers published their findings in the journal Science Advances.
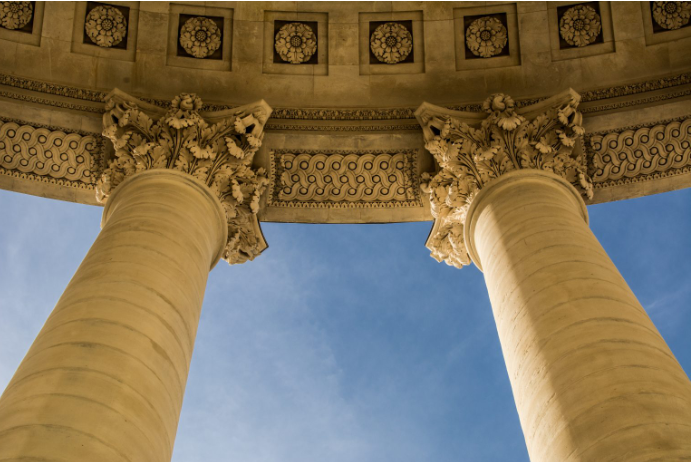
Lime clasts were key components of Roman concrete
Researchers have assumed that the key to Roman concrete’s durability was based on one ingredient: the volcanic ash from the area of Pozzuoli on the Bay of Naples. However, under closer examination, these ancient samples also contain small, distinctive, millimetre-scale bright white mineral features. These white chunks, known as “lime clasts,” originate from lime, another key component of the ancient concrete mix.
“Ever since I first began working with ancient Roman concrete, I’ve always been fascinated by these features,” stated Professor Admir Masic. “These are not found in modern concrete formulations, so why are they present in these ancient materials?”
The new study suggests that these tiny lime clasts gave the concrete a previously unrecognised self-healing capability.
The new study suggests that these tiny lime clasts gave the concrete a previously unrecognised self-healing capability
“The idea that the presence of these lime clasts was simply attributed to low-quality control always bothered me,” says Masic. “If the Romans put so much effort into making an outstanding construction material, following all of the detailed recipes that had been optimized over the course of many centuries, why would they put so little effort into ensuring the production of a well-mixed final product? There has to be more to this story.”
And upon further investigation and characterisation of these lime clasts, researchers gained new insights into how these lime clasts functioned and how they were instrumental in the continuing structural integrity of Roman concrete.
Is hot mixing the answer?
Historically, it was thought that lime was combined with water when incorporated into Roman concrete – a process called slaking – but this alone could not account for the presence of the lime clasts. “Was it possible that the Romans might have actually directly used lime in its more reactive form, known as quicklime?” Masic proposed.
Masic’s team determined that the white inclusions were, indeed, made out of various forms of calcium carbonate. A spectroscopic examination provided evidence that these had been formed at extreme temperatures, as would be expected from the exothermic reaction produced by using quicklime instead of, or in addition to, the slaked lime in the mixture.
The team has concluded that hot mixing was the key to the super-durable nature.
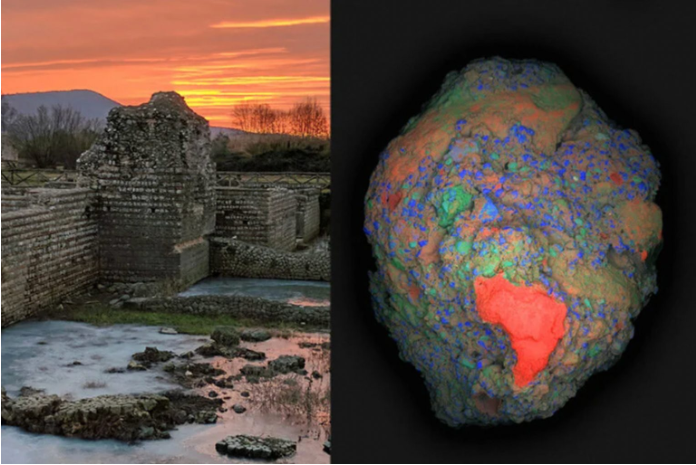
What are the benefits of hot mixing?
According to Masic, the benefits of hot mixing are twofold: “First, when the overall concrete is heated to high temperatures, it allows chemistries that are not possible if you only used slaked lime, producing high-temperature-associated compounds that would not otherwise form. Second, this increased temperature significantly reduces curing and setting times since all the accelerated reactions allow for much faster construction.”
During the hot mixing process, the lime clasts develop a characteristically brittle nanoparticulate architecture, which creates an easily fractured and reactive calcium source. This architecture allowed the critical self-healing functionality, Masic and team proposed.
As soon as tiny cracks start to form within the concrete, they can preferentially travel through the high-surface-area lime clasts. This material can then react with water, forming a calcium-saturated solution, which can recrystallize as calcium carbonate and quickly fill the crack, or react with pozzolanic materials to strengthen the composite material further. These reactions take place spontaneously and automatically heal the cracks before they spread. Previous support for this hypothesis was found by examining other Roman concrete samples that exhibited calcite-filled cracks.
To prove that this was indeed the mechanism responsible for the durability of the Roman concrete, the team produced samples of hot-mixed concrete that incorporated both ancient and modern formulations, deliberately cracked them, and then ran water through the cracks.
Within two weeks, the cracks the team had observed had completely healed, and the water could no longer flow. An identical chunk of concrete made without quicklime never healed, and the water flowed through the sample. As a result of these successful tests, the team is working to commercialise this modified cement material.
“It’s exciting to think about how these more durable concrete formulations could expand not only the service life of these materials, but also how it could improve the durability of 3D-printed concrete formulations”
“It’s exciting to think about how these more durable concrete formulations could expand not only the service life of these materials, but also how it could improve the durability of 3D-printed concrete formulations,” concludes Masic.